August 31, 2021
If you are as fastidious about your workstation as Martha Stewart is about her table setting, you always ensure that there is never a screw out of place or a wobbly chair at your desk. Framing fasteners are the vital connectors that keep materials and machinery secure. For example, when we commit to piecing together DYI Ikea furniture, we are scrupulous in employing the myriad bits and pieces as directed. While we may fret and fume during the assembly process, nuts and bolts ensure the end product looks and functions as advertised.
Bolt vs. Screw
Bolts are externally threaded fasteners installed with the use of proper nuts that are fitted using torque. Bolts are typically used to couple unthreaded objects. The threads spiraling on the circular surface of the bolts provide exceptionally sturdy bonds in conjunction with a nut.
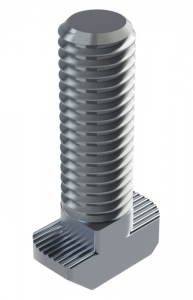
Screws are also externally threaded fasteners. They can be inserted into premade holes or perforated surfaces and sometimes create threads during installation.
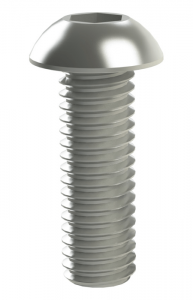
Roots of the Bolt
Considering their modest size, bolts perform an impressive task. They are essential in keeping the parts and pieces together in things big and small—from humdrum kitchen appliances to concrete pillars supporting grand buildings.
The inception of the bolt in a rudimentary form can be traced back centuries. The thread configuration on the bolt is believed to have originated around 400 BC, when it was used for apparatuses like a grape press for making wine. In the 15th century Johann Gutenberg, a goldsmith from the riverside town of Mainz, Germany, used screws in building his printing press. Gutenberg’s press was a pivotal invention that made books widely accessible. “The press was built around the traditional screw press, a precursor to today’s drill press, with an added matrix on which individually cast letters and symbols could be arranged from the desired text” (from “Treasures of the McDonald Collection”).
The Industrial Revolution accelerated the development of the nut and bolt and strengthened their significance in construction and engineering. According to the History of the Nut and Bolt Industry in America by W.R. Wilbur, the first machine for making bolts and screws was crafted by Besson in France in 1568. Besson subsequently made a screw-cutting gauge or plate used on lathes. In 1641, Hindley of York in England improved Besson’s design and thereby increased its popularity.
The Carriage Museum of America has documented the history of nuts and bolts in painstaking detail. It credits Micah Rugg, a blacksmith in Connecticut, for manufacturing nuts and bolts in America. According to their research, Rugg took a partner, Martin Barnes, and together they founded the first company to manufacture nuts and bolts in the country.
During World Wars I and II, the variations in screw threads across countries proved to be a challenge. In 1948, America, Canada, and Britain decided to use the Unified thread as the new standard for countries that subscribed to imperial measurements. It was akin to the DIN metric thread developed in Germany in 1919. The larger root radius of the Unified thread proved to be more efficient than the DIN metric profile. Ultimately, the ISO metric thread became the norm in all industrialized countries.
Updates to the ISO standard and the modern metric property classes describe a bolt’s strength and the test methods used to establish its properties. Over the years, steel—traditionally used to manufacture bolts— has been replaced by lighter materials like aluminum and even more exotic materials such as titanium to keep pace with evolving uses and demands.
The Advent of the T-bolt
George R. Lang of Cincinnati is credited for “inventing” the T-bolt (Iron Trade Review, Vol. 38, 1905, p. 31). It was initially used on boring mills and other machine tools. The material being worked on was clamped to the machine by threaded bolts inserted into T-slots on the bed’s surface. When the type of work changed, appropriate bolts of the correct length were needed. Often, new bolts had to be made for the task. Lang’s invention of the T-bolt eliminated the arduous process of forging new custom bolts.
Versatile and sturdy, the T-bolt’s head is configured such that it can be inserted into a recess or slot. The T-bolt can easily be inserted at any point in the slot and can be used in various applications. For example, the T-bolt could be the ideal choice if one were making a feather board for a table saw or where clamps are necessary. T-Bolt clamps ensure a reliable seal in large-diameter applications and high vibration settings like machinery, irrigation, and transportation trucks. The T-bolt also comes in handy when an existing fixture requires an additional clamping point.
At FramingTech, T-bolts are commonly used as fasteners in the assembly of our various metric and inch extruded aluminum T-slot fabrications. For that purpose, we offer a wide variety of T-bolts in various sizes.
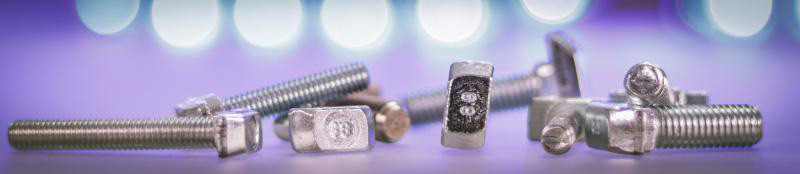